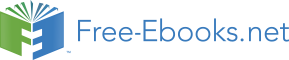

CHAPTER-1
1-INTRODUCTION
1.1 BACKGROUND OF THE STUDY
Three main sectors which contribute to the Indian economy are agriculture, industrial and service, we cannot ignore as in 2005-06 GDP growth was 8.1 % with Industrial sector to 9.4 %, agriculture growth 2.3%1. So Industrial sector has lot more contribution to the India’s Economic, as Industrial goods are defined as companies which buy products and services to help them produce other goods and services 2 . Industrial goods deals with3: accessory equipments (ex. hand tools, lift trucks), business service(ex. banking and maintenance), installations (ex. furnaces, refractory) ,parts ,raw materials, semi manufactured goods and supplies(maintenance, repair and operating supplies). when installations were furnaces are built up of both metallic and non metallic parts with the application of heat resisting non metallic materials used in it are called "Refractories”4,.As such steel plants, cement rotary kilns or a glass melting furnaces could never produce finished goods without the application of Refractory products. The below table 1 indicates Refractory products in India directly assist in the current production of about 24 mt of steel, 70 mt of cement clinker, over 9 lakhs tonnes of glass and about 8 lakhs tonnes of non- ferrous metals in the country.5
Contribution of Refractory Products in different Industries are as follows:6
Even though, the contribution of Refractory industry in India is 4% of the Global Market7, but for the last four to five years Refractory industries have been in good progress for exporting its products ex. export has increased from Rs. 314 Crores in 2006-2007 to about Rs. 452 Crores in 2007-20088(IRMA). Even though the export competitiveness and market of refractory in India are small in size compared to its counterparts elsewhere. The total 120 refractory industries which are spread over many states mainly Tamil Nadu, West Bengal, Bihar, Orissa, Madhya Pradesh, Maharastra, Gujarat and Rajasthan9. But if we take a look on the share of Refractory Industries of different regions in the world market were Asia/Pacific 40% ,Eastern Europe 23% ,Latin America 4% NAFTA (USA,Canada and Mexico) 14% ,Western Europe 15% and Others (Africa and the middle East) 4%10.
Moreover the aggregate production capacity of India is 1,500,000 metric tonnes per year- actual production however is between 700,000 and 1,000,000 metric tones 11 per annum and in worldwide refractory market estimated to be 22 to 25 million tonnes - as opposed to a production capacity of approximately 40 million tonnes.12
As in domestic market due to the new upcoming of four Greenfield and one expansion project of Tata Steel, Essar, Posco, Arcelor Mittal and SAIL set to take off in Orissa in the next three to four years, refractory manufacturers in the state are in a mixed mood. So the future scenarios of these refractory manufacturers, mostly dependent on steel plant projects, which would keen in meeting the demand points and stand more viable logistically too. Orissa is one of the state has quite a few reputed refractory manufacturers capable of making quality refractory products to stand themselves to compete not only domestically but also globally with their specialty products . Tata Ref Ltd(No. 1 Refractory Manufacturer in India), OCL Ltd, IFGL Ref Ltd(No.1 Refractory Exporter), Sarvesh Refractories Pvt. Ltd, and Manishri Refractories and Ceramics Ltd are the major players who are operating in the state for a long time.
On the other side, influx of Chinese refractory is a major concern for these refractory manufacturers in India. But with current import trends from China, these refractory manufacturers looking worried as around 20 percent of the refractory produced in India are imported and most of the imported refractories are sourced from China, according to a spokesperson from the Indian Refractory Manufacturer's Association (IRMA). Around 0.3 million tons of refractory was imported in 2006-07 on an annualized basis, these is a big concern for the small players operating in the domestic markets.
In the below Table 2. Depicts the Steel industry is the highest consumer of refractory which consumes around 12 kg of refractory per ton of steel produced. After steel, aluminum consumes 4 to 5 kg of refractory per ton of aluminum produced. Cement consumes around 0.8 to 0.9 kg of refractory per ton. Other than steel, aluminum and cement, consumption of refractory in other industry is insignificant.
(Sources: Steel Insights)
This study has been conducted because of the recent changes in the refractory industry, which has given a competitive look in the domestic as well as international market. As such there has been lot of technical papers published but not on the marketing aspect which is going to be the key factor for survival in the long run of the business. During the past two decades the refractory industry has been changing at a rapid pace with new materials, production and application techniques. It is directly reciprocal to the changes in the refractory industries , the changes in the manufacturing sectors also need to be followed. So Indian Refractory makers have started to think globally not only in respect to product wise but also in market wise too. In comparison to other industries the refractory industry is small and very specialized one but it’s contribution cannot be ignored to the Indian economy which is very sad to say that it has never received its due recognition because of its insignificant size compared to its key user industries like steel, cement and aluminum.. This study would offer information of the Indian refractory makers in Orissa trying to market their products in the international arena along with the important features which would reflect how competitive refractory industries in Orissa against the world trends.
REASONS FOR THE STUDY AND ITS IMPORTANCE
The purpose of this study is to show the varieties of equipment and processes in the refractories industry, their individual functions, and their importance to the overall metal and nonmetal consumer and producer industries. The refractories industry plays an important role in making materials usable. Refractory is needed to cause desired changes in the metallurgical structure and hence the properties of metal parts. Properties of most metals and alloys can be affected by heat treatment. Ferro-alloys, particularly steels, undergo the most dramatic changes in properties. Generally, the most stable steel structures are produced when steel is heated to a high temperature and then slowly cooled. This is called annealing or normalizing. The process of heat treatment performs multiple functions as are needed for individual cases. In some cases, it releases stress, strain, and fatigue so that the material will work normally. In other cases, it alters the structure so that the material's properties will improve. As an example, parts made from glass and some ceramic cannot be used without proper annealing. They will simply shatter under residual stress. All of these functions are carried out in heat treating furnaces of various kinds, shapes, and sizes.
There are two components of the refractory industry. One component of the industry involves the manufacture of the heat treating furnaces and the other the utilization o the furnaces for heat treating purposes. A number of furnace manufacturers also offer custom heat treating operations. Since the total heat treating industry is very large and broad (a total of 750 to 850 large, medium, and small companies), with a total turnover of about $15 billion, this report will deal only with heat treating furnace manufacturers who make the furnaces and sometimes offer customized heat treating services.
1.2 RESEARCH OBJECTIVES
Refractory companies in Orissa emerging even stronger with the opening up of the economy and now command a competitive position not only in the Indian refractory industries but also competing globally with better competitive advantages. This study intends to find out the competitive advantages which few of the largest Indian refractory companies has created over time and how have they adapted to the changing environment. A thorough analysis of the leading companies particularly in Orissa among the 5 refractories industries we have identified IFGL Ref Ltd and Tata Ref Ltd has been conducted in order to identify the future potential of these companies and to understand the way in which it could sustain its competitive advantage not only domestically as well as globally.
The Indian refractory manufacturers are also dependent on China for the supply of important raw materials such as brown bauxite, fused alumina and other items. Without Chinese material, the domestic players either have to import similar materials at more prices from other countries or have to develop inferior grade domestic source at costs which is not recoverable from the customers, which indirectly have effect on the quality of the product that has an impact on the performance. As performance is directly related to the cost realization for the refractory industries.
So to reduce the cost of production by the steel industries are not encouraged to develop one refractory source for strategic alliance as the specific cost of refractory in the blast furnace, coke-oven and converter route is only Rs 350 per ton of liquid steel produced, which is only 1.9 percent of the cost of producing steel. (Sources: Steel Insights)
Michael Porter, (1985) opines that competitive advantage means creating unique capabilities and strengths, which can be defended against imitations from rival firms (Porter, 1985). It is learning lesson for the Refractory Industries to follow the path of competitive advantage to survive in the long run of competition.
Wharton (1997) on the other hand suggests that a company in various ways can obtain competitive advantage but it is very important for us to define the scope. Research examines the competitive advantage created by IFGL Ref Ltd and Tata Ref Ltd vis a vis the other industry players (Indian Refractory Makers Association). Public sector policies can create and help to sustain competitive advantage for firms, or can undermine and even destroy advantages (Wharton, 1997), thus it is necessary to understand the policy issues governing the industry.
AUDIENCE FOR REPORT
The report is meant for a variety of people who are interested in the heat treating of metals like iron, steel, and nonferrous metals, and of other materials like glass and ceramic parts. Refractory manufacturers who makes furnaces of various types will have detailed information about their industries. The refractories industry has a major impact on ancillary industries such as those involving the manufacture of gas and oil heating systems, electrical resistance and induction heaters, and controls and switches for heating, furnace atmosphere, and the total process. Manufacturers of salt bath, ovens, and lehrs, etc. will also be interested in the report. Other people who are inclined to look at the potential of this industry will also benefit from this report. Investment-oriented people will be able to evaluate the potential of refractory or the furnace manufacturing component of the user industries.
SCOPE AND CONTENT OF REPORT
The scope of the report will be limited to heat treating furnaces for ferrous and nonferrous metals, and annealing furnaces for glass and ceramics. The report will provide a comprehensive report about the different types of furnaces with regard to their sizes, shapes, capacities, and price ranges. The report will include information on the heat insulating refractories for different types of furnaces. It will also discuss the different types of heating systems available along with the modern control systems.
The report includes information regarding the manufacturers-the leading companies, their locations, products, capabilities, asset values, and some of their officers. It also identifies the different types of furnaces and ovens that each individual company makes. The report presents the current market of the refractory industries and indicates the future potential for the next 5 years. The report also discusses the domestic as well as world market for the refractory industries and indicates current conditions and future prospects.
METHODOLOGY AND INFORMATION SOURCES
The report is presented in a systematic way by identifying the refractory manufacturers and their customers along with their current and future market potential. The information for the report has been derived from a variety of sources. The theoretical aspects of the heat treatment processes have been provided from books on fundamental principles on heat treatment. A major amount of information has been provided from the Indian Refractory Makers Association(IRMA) and Technology Information, Forecasting and Assessment Council (TIFAC) . Actual information has been gathered mostly from dialogue with furnace manufacturers and users as well as makers of heating systems and controls. Other information has been provided by discussion with Dr. A.K Chattopadyay of IRMA and the author's personal experiences in using heat treating furnaces and processes. Information in the section on International Refractory markets and financial aspects has been obtained from different websites like American Ceramic Society and South East Asian Iron and Steel Institute.
1.3What are Refractories?
"Refractory" items according to any standard english dictionary are materials which are hard to work with, and are especially resistant to heat and pressure. In practical terms, refractories are products used for high temperature insulation and erosion/corrosion and are made mainly from non-metallic minerals. They are so processed that they become resistant to the corrosive and erosive action of hot gases, liquids and solids at high temperatures, in various types of kilns and furnaces.
Basalt is a naturally occurring siliceous refractory product. It was formed many, many years ago - and is still being formed in lava flows from volcanic eruptions - under the natural geological forces of heat and pressure. Modern refractory production is largely a replication of this process of forming naturally-occurring (or synthetic) non-metallic mineral oxides (and some non-oxides like carbides or nitrides) under the bonding conditions of high heat and pressure. Of course with technological progress, alternative bonding techniques, such as with chemicals, cements, resins, etc. have also developed.
Because refractory products are so resistant to heat, erosion and corrosion, they are typically used in any process involving heat and corrosion such as in kilns and furnaces. According to the main chemical component, i.e. fire clay, or magnesia, or zirconia, etc. they are commonly known as alumino-silicate or acid refractories, basic refractories, and neutral refractory products.
In physical characteristics, refractories typically have relatively high bulk density, high softening point and high crushing strength. They are produced as standard bricks, or as shapes (including hollow-wares) or as granular or unshaped or monolithic products.
The principal applications of refractories are in iron and steel industries, cement, glass, non-ferrous metals, petro-chemicals and fertilizer industry, chemicals, ceramics and even thermal power stations and incinerators.
The development and application of refractories for various industries, testing procedures of properties and so on are covered in the English language, by a number of well-known technical journals, such as The Bulletin of the American ceramic society, Taikubutsu overseas, Interceram, Ceramic news, Refractories applications, IRMA Journal, Transaction of the Indian ceramic society, Metal news, etc.( http://www.irma.org.in/refractories)
1.3 IMPORTANCE OF THE REFRACTORY INDUSTRY
The boom in the Indian steel sector may see a boom in yet another industry, that of refractories. Though steel makers are yet to grant due recognition to this critical material, they have slowly begun to realize its importance.
The cutting edge for refractories in steel making lies in the fact that it can make a huge difference in the cost of production. At the refractory manufacturers' end, the potential is enormous but concerns are serious. If they have to cash in on the boom, they have to work out an optimal strategy. Optimism, however, runs high.
The industry is going through an exciting and complex phase. On one hand, refractory makers are adding capacities with the hope that demand from the steel sector will rise at a fast pace. On the other hand, none of the major announced Greenfield projects are yet to get off the ground.
So an obvious question hovering around everyone's mind is: What lies ahead for the Indian refractory makers? A popular notion that prevails about the installed capacity is the fact that India has excess installed refractory capacity. (Sources: Steel Insights)
The Indian refractories market is growing at an 8-10% per annum and is currently pegged at Rs. 3,100 crore3. About 20 years ago the consumption of refractories per ton of steel was 30kg and now this has come down to 7-8kg in some of the more efficient steel plants. The industry is expected to grow with the growth of the country’s economy and the Indian government’s continued attention to infrastructure development. The steel industry, which is the single largest user of refractories, is likely to grow up to 150 million tons by 2015. The cement and aluminum industries are also expected to grow exponentially. The use of refractories in steel production can bring about a huge reduction in the production cost.
With a 20 lakh tons per annum aggregate production capacity as on December 2006, it has gone up by about 5-10% in 2007; the capacity utilization is 11.5-12lakh tons per annum or about 60 percent4 . The production capacity has also increased by about 10% in 2007. By 2010, with an increase in the steel production, the demand for refractories is expected to touch 12 lakh tons per annum5. The below figure depicts global steel production:
Sources:Yoke Fong, Commercial Director Refractories Asia, Qingdao Almatis Co., Ltd, Shanghai, China; adapted from her presentation at the 7th Chinese Industrial Minerals Conference, 9-11 October 2007, Dalian. Furthermore, about 75 million tons per annum of the cement capacity is likely to be added by 2010. The below figure depicts the global cement demand:
Sources: http://www.bricks-n-mortar.com/2008/08/web-share-world-cement-demand-forecast.html.
And moreover world glass demand cannot be ignored as depicted in the below figure:
As a result, the domestic companies are currently expanding so as to cater to the rising demand from the user industry. The Indian refractories makers association which represents this industry on the national level is trying to position the Indian refractories as “between China on the one hand and Europe on the other. Indian refractory industries eyeing overseas demand of products as in 2006-07, the exports of Indian refractory were Rs. 313.65 Crores7.
Sources:www.irma.org.in
There are two options for the Indian refractories manufacturers. One is to go in for a price war with the Chinese makers however this would reduce their already small profit margins or there could be more focus on exports, which is what the bigger players are doing already.
3. Roy, A.S., “Refractory industry hard pressed for inputs”, Business Line, May 7, 2008.http://www.thehindubusinessline.com/2008/05/07/stories/2008050752461000.htm. Accessed on May 16, 2008.
4. http://www.blonnet.com/2008/02/08/stories/2008020850992300.htm. Accessed Feb 25, 2007.
5. “Refractory industry in a limbo amidst steel boom, Feb 18, 2008. http:// www.mjunction.in/market_news/metals/refractory_industry_in_a_limbo.php. Accessed on March 15, 2008.
6. http://www.steelonthenet.com/production.html. Accessed on Nov 20, 2007.
7. http://www.irmaindia.org/serv.html. Accessed March 12, 2008.
History of the Refractory Development in India
Recent Milestones in Refractories Development
Unidirectional Gas Purging Elements
Alumina Carbon Ladle Bricks and Slide Gate Refractories
Mullite Bricks for Blast Furnace & Stoves
Dry Basic Ramming Mass, Gunning materials for Converters,
Spraying Mass for Tundish
Pitch-Bonded Tempered Dolomite Bricks
Alumina Carbon Silicon Carbide BF Trough Mass
Alumina Zirconia Slide Gate and CC Refractories
Pumpable Refractories
Nitride-bonded silicon carbide products
Sources: http://www.irma.org.in/refractories/milestones.html
Typical Product Specification of Indian Refractories
Some typical specifications of Indian refractories commonly used in the furnaces and kilns in steel, cement, non-ferrous metals and glass industries are given below. These are illustrative and do not cover the full range of products and some of the improved items which have been recently developed.
Fire Clay Bricks/Shapes (Steelworld June 2006 10-13)
These are basically aluminosilicate refractories possessing alumina not exceeding 42%. Fire clay refractories earlier used to find use in lining of blast furnaces for hearth and bosh portion due to the dense structure, reheat shrinkage, resistance to slag and load characteristics of these bricks. How ever, today, the dense low heat duty fire clay refractories find use in top part of the blast furnace where abrasion resistance is required and upper in wall portion where slight slagging action & abrasion resistance are necessary, intermediate duty fire clay bricks are applied. Though these are the most economical variety of refractories but suffer from poor slag resistance & low refractoriness characteristics. In many steel plants, these find extensive use in lining of soaking pits & reheating furnaces, bottom pouring refractories for steel casting, safety lining of the steel ladles and kilns in cement industry due to their good insulating, spalling resistance, dense structure preventing erosion characteristics.
High Alumina Bricks/Shapes :
The change in the quality of the raw materials, increased productivity and higher temperature and increased campaign life in iron/steel making arena resulted in drastic reduction in consumption of fire clay products and evolution of high alumina refractories. 60%-72% alumina mullite bricks are used in h