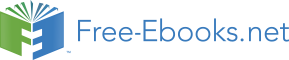

Section I. COAL
2-1. General.
Coal is a mineral originated from decayed trees,
ferns, and other types of vegetation. It is composed
of varying proportions of carbon, hydrogen,
oxygen, nitrogen, sulfur, and several noncombusti-
ble materials which make up the ash. The ash is
composed mainly of silica, alumina, iron, lime, and
small quantities of magnesia. Coal used as com-
mercial fuel consists primarily of volatile matter,
fixed carbon, sulfur, ash, and water. The types of
coal used at military installations are anthracite,
bituminous, sub-bituminous and lignite. Table 2-1
gives the heating value for these coals.
Section II. FUEL OILS
2-2. General.
b. Residual fuel oils. When marketed as a fuel,.
Fuel oils are derived from crude petroleum. Crude
the “bottom” or residual material from the distil-
petroleum is a mixture of hydrocarbons and small
lation process is called residual fuel oil. Since crude
amounts of nitrogen, sulfur, and vanadium; the
petroleum from various sources differ widely in
amount of each substance present varies with the
composition, there is considerable difference in
petroleum source. There are two types of crude pe-
these oils. In general, they are heavy, dark and
troleum available in the United States, paraffin-base
viscous compared to the lighter and more fluid dis-
and asphalt- or naphthene-base. Paraffin-base
tillate oils.
crudes are found in the Appalachian mountain
c. Commercial grade fuel oils. Commercial-
range and in the Midwest. Asphalt-base crudes are
grade fuel oils are generally classified according to
found in Texas and California. Paraffin-base crudes
physical characteristics and use. Current standards
yield many valuable lubricating oils. The asphalt-
designate five basic grades of heating fuel oil: Nos.
base crudes furnish the major part of commercial
1, 2, 4, 5, and 6.
fuel oil used in the United States. The various
(1) No. 1 oil. This is a light volatile distillate
products derived from petroleum, including fuel
with essentially the same burning characteristics as
oils, are separated by fractional distillation. This is
kerosene. It is generally used in vaporizing pot type
a process by which liquids with different boiling
burners under domestic heating boilers and
points are separated from solution by repeatedly
furnaces. The average heating value is approxi-
evaporating and condensing portions of the
mately 135,000 Btu per gallon.
mixture.
(2) No. 2 oil. This is slightly heavier distillate
than No. 1 oil. It is used as domestic fuel oil in
2-3. Classification of fuel oils.
some types of vaporizing burners and in high and
low pressure atomizing burners. Its average heating
In general, fuel oils can be divided into two major
value is approximately 139,000 Btu per gallon.
classifications: distillate and residual.
(3) No. 4 oil. This oil may be 100% residual
a. Distillate fuel oils. When the fractional distil-
material. However, for marketing purposes, it is
lation process is applied to crude petroleum, the
generally blended with sufficient distillate stock to
gaseous and light substances boil off first, followed
meet viscosity and flashpoint requirements for the
by gasoline, kerosene, and then light and heavy
grade. Grade No. 4 oil, like grades No. 1 and 2,
distillate fuel oils (gas oils).
2-1
TM 5-642
atomizes under normal conditions without heat.
characteristics. The cetane number, a measure of
The approximate heating value is 145,000 Btu per
the ignition quality of the fuel which influences
gallon.
engine roughness, varies from a minimum of 40 for
(4) No. 5 oil. This oil, like No. 4, can be a
grades 1-0 and 2-0 to 30 for grade No. 4-0. Diesel
straight residual product; but it is also marketed in
fuels are normally used for firing stationary engines
many areas as a blend of distillate and residual
and not for heating.
stocks. No. 5 oil has medium viscosity. Installations
that use it generally have oil heating facilities. The
2-4. Oil tanks.
heating value of No. 5 oil is approximately 150,000
Tank installation is largely governed by local con-
Btu per gallon.
ditions. Listed here are the principles of tank in-
(5) No. 6 oil. No. 6 oil is a high viscosity, resid-
stallation that give greatest freedom from service
ual material. It is used in large commercial and in-
problems. Adhere as closely to these recommenda-
dustrial steam generating plants and in certain in-
tions as local conditions permit.
dustrial processing operations. Its use requires pre-
a. Indoor or elevated outdoor tanks. Whenever
heating facilities for transportation unloading,
possible, install single-pipe gravity oil feed inside or
pumping, and atomization. The heating value
elevated outside tanks. (See figure 2-1.) Use a 1/4-inch
averages approximately 154,000 Btu per gallon.
globe valve at the tank rather than a larger valve,
d. Diesel fuel oils. Diesel fuel oils vary widely in
which may cause “tank hum”.
b. Tubing. For all installations, use a continuous
d. Underground outside tank. Install under-
piece of ½-inch copper tubing from the oil tank to
ground outside tanks according to the following in-
the burner and a similar piece for the return when
structions and figure 2-2:
required. The principle is to minimize the number of
(1) Install a continuous piece of copper tubing
joints and to thus minimize the possibility of air or
from a point 3 inches above the bottom of the tank
oil leaks.
up through a compression fitting in the top plug,
over into the basement, and into an approved check
c. Overhead piping. For inside installations
valve. Where possible, drop this feed-line inside the
where it is necessary to run the piping between the
building to a point level with the bottom of the tank
tank and burner overhead (when the burner is either
before the check valve.
above or below tank level), the two-pipe system is
(2) Use a ½-inch IPS straight compression con-
recommended. This system requires the use of a
nector (for ½-inch tubing) for running the ½-inch
two-stage pump.
copper tubing through the tank cap. Drill out the
2-2
TM 5-642
inside of the connector, allowing the tubing to slip
two lines and any agitation caused by return oil is
completely through; drill and tap the tank cap for
safely away from the suction line.
½-inch IPS to receive the connector. Slip the tubing
(4) A 2-inch fill line and 1¼-inch vent line are
through the connector and down to the proper
recommended. Carry the vent well above ground
point 3 inches above the tank bottom. Tighten the
and terminate it with a weather-proof cap. Pitch
connector, locking the tubing in the proper
the vent line down toward the tank.
position.
(5) Use special pipe dope on all iron pipe fit-
(3) Install the return line in the opposite end of
tings that carry oil.
the tank, using the technique described for the
(6) Treat all underground outside tank and
suction line, above. Carry it to within 5 inches of
piping surfaces with a standard commercial
the bottom. This creates an oil seal between the
corrosion resistant paint or preparation.
Section III. NATURAL GAS
2-5. General.
are not normally included in a consumer*s gas
Natural gas is the most commonly used gaseous
system installation. A gas handling system consists
fuel in small heating systems. Natural gas is usually
of all or some of the following items:
odorless and requires the addition of odorants to
a. Pressure reduction station. This is used to
permit detection. According to its content of hy-
reduce the supply pressure and maintain a relatively
drogen sulfide it is known as “sweet” or “sour”.
constant pressure despite variations in supply.
Sour natural gas is normally thought of as gas
b. Low pressure safety shut-off valve. The func-
containing more than 1.5 grains of hydrogen sulfide
tion of this valve is to interrupt gas flow to burners
per 100 cubic feet of gas. Its heat value varies from
if the supply pressure drops below a predetermined
approximately 950 to 1,150 Btu per cubic foot.
value.
c. Flow meter. This meter indicates and records
2-6. Gas handling and storage.
the volume of gas consumption.
The supply company normally delivers natural gas
to consumers by pipeline. Storage tanks therefore
2-3
TM 5-642
d. Pressure and temperature gauges. These aid
2-7. Gas handling precautions.
the operator to control and supervise operation of
Natural gas is toxic, and its presence in appreciable
the equipment.
quantities is a serious health hazard. Gas diffuses
e. Vents, drains, moisture separators, and relief
readily in air resulting in possibly explosive
valves. Vents are used to purge the system and
mixtures. Because of these characteristics, be sure
remove all air and inert gases during filling proce-
dures. Moisture separators and drains remove con-
there are no leaks present and exercise caution
densate from the system; relief valves prevent ab-
when lighting gas fired equipment.
normally high gas pressure if the system reducing
valve malfunctions.
Section IV. LIQUEFIED PETROLEUM GAS
2-8. General.
b. Specific gravity. Natural gas is lighter than air
Because of the special characteristics of liquefied
and in case of a leak, will float away and be
petroleum gas (LPG), it must be handled and stored
dissipated in the air. However, vapors from lique-
with great care in properly designed tanks and
fied petroleum gases are heavier than air and
equipment. If handled carelessly, whether through
therefore tend to settle in low points. In making
failure to understand its characteristics or for other
installations, this must be carefully considered and
reasons, this fuel presents a definite hazard to life
bottom ventilation provided in basements in which
and property.
a furnace or appliance is used. Basement installa-
tions are definitely not recommended and must not
2-9. Characteristics.
be made unless absolutely necessary and all safety
The principal commercial products are butane, iso-
aspects are considered.
butane, and propane. They are closely related, are
all derived from natural gas or petroleum refining
2-10.
Specifications.
gas, and are on the border line between a liquid and
a. Propane. As a gas (60F at 14.7 psi), the heat-
a gaseous state at atmospheric pressure.
ing value of propane is approximately 2,500 Btu
a. Vaporizing point. At ordinary atmospheric
per cubic foot. As a liquid (-45F at 14.7 psi), the
pressure with necessary heat of vaporization added,
heating value of propane is 91,800 Btu per gallon
butane will boil at 31F. The boiling point of
or 21,560 Btu per pound.
isobutane is 10F and the boiling point of propane is
b. Butane and isobutane. As a gas (60F at 14.7
-44F.
psi), the heating value of butane and isobutane is
(1) Under pressures higher than atmospheric
3,100 Btu per cubic foot. As a liquid (12F at 14.7
the boiling points are higher than at atmospheric
psi), the heating value is 102,400 Btu per gallon, or
pressure. The fuel, if placed under pressure, can be
21,500 Btu per pound.
held in a liquid state and transported by tank car,
truck or cylinders. However, LPG must be in the
2-11.
LPG storage and handling.
vaporized or gasous state to be used as a fuel.
(2) To change these petroleum products from
At Army installations, gas handling and storage
a liquid to a gasous state the liquid must be main-
equipment upstream of the tank pressure reducing
tained at the boiling point and the latent heat to
valve are usually the property of the gas supplier.
produce vapor must be added. For small installa-
The pressure reducing valve and all equipment
tions, heat from the atmosphere in warm climates
downstream is government property. This may in-
or from the ground in colder climates, is usually
clude a pressure reducing station, low pressure
sufficient to vaporize the liquid. In cold climates,
safety shutoff, flow meter, pressure and tempera-
where temperatures of the liquid will drop below its
ture gauges, vents, drains, moisture separators and
boiling point, a vaporizer must be used; that is, the
relief valves. Do not tamper with nongovernment
liquid is passed through a heating device which will
property. Most fuel supplied as LPG is commonly
apply sufficient heat to vaporize it. The gas flows
designed to conform with the properties of pro-
from the tank through a valve and pressure
pane. Equipment designed for handling and storing
regulator. The regulator reduces tank pressure to
butane (a lower pressure gas under similar op-
the low pressure required to operate appliances.
erating conditions) must not be used for propane.
Although pressure on the tank may be 100 psi, the
The vapor pressure of propane at 60F temperature
pressure regulator reduces this pressure to about 6
is 92 psig; if the temperature rises to l00F the vapor
to 8 ounces, or less, per square inch.
pressure increases rapidly with temperature rises.
2-4
TM 5-642
Equipment for storing and handling propane is
Most petroleum derivatives such as kerosene, gaso-
rated at 250 psi to provide a reasonable margin of
line, natural gas, or LPG are combustible and, when
safety.
not handled carefully, can be explosive and
a. LPG storage. LPG is stored in pressure tanks
dangerous. When properly handled, suitably
with the gas vapor filling the upper portion. Tanks
housed, and controlled, they can be used safely.
are fitted with a liquid line and a vapor line con-
c. LPG piping. Liquefied petroleum gas acts as
nected to the vaporizing equipment (if used) and a
a solvent of all petroleum products; for that reason,
liquid line and a vapor line connected to the un-
use a special pipe dope containing no mineral oils
loading pit. In addition, the tank is usually provided
or rubber. Because gases revert to their liquid state
with a safety valve, a thermometer well, a pressure
when cooled below respective boiling points, bury
gauge, a 90 percent full indicator, and a sliptube
gas lines below the frost line. Never run LPG lines
type of gauge for determining the liquid level in the
under concrete floors, and run under buildings only
tank. Any valve pit or other below grade location
when absolutely necessary. Bury supply lines
where leakage of gas or liquid might occur, is
parallel to and at least two feet away from building
vented by a pipe stack tall enough to carry off the
walls. Install separate takeoffs and risers for each
vapors. Because LPG is heavier than air, the vent
appliance and enter the building at the nearest
stack must have a mechanical exhauster operated
practicable point to the appliance or furnace.
by either power or wind.
Whenever possible, run lines inside buildings using
b. LPG handling precautions. When handling
a single length of pipe without joints.
LPG, take the following precautions:
d. Installation and control of LPO systems. For
(1) Any work required in a fume-filled or con-
furnace installations, pressure regulators are not
taminated area must conform to all safety regula-
required at the furnace. Take the pressure reading
tions to eliminate personnel hazards. LPG is odor-
at the furnace manifold and set the pressure at the
less, colorless, tasteless; it is odorized with the
regulator on the liquefied petroleum tank or
same odorants as natural gas. Although LPG is not
atomizer. Furnaces using LPG require a manifold
poisonous, exposure to a room or pit full of gas
pressure of 11 to 13 inches water gauge, whereas
causes a synthetic intoxication; and if exposure is
with natural gas, a pressure of 2.5 to 5 inches water
prolonged, asphyxiation (smothering) results. LPG
gauge is required. Follow manufacturer*s
is heavier than air and will hang to the floor or
recommendations covering manifold pressures for
ground.
liquefied petroleum gas at the furnace. If gas lines
(2) Avoid contacting the liquid with the hands
serving other appliances, such as water heaters,
or any part of the body. When LPG is released from
space heaters, or cooking appliances are taken from
a container and evaporated, it absorbs heat from
the line serving the furnace, an approved double-
anything it touches. Therefore, any part of the body
diaphragm, low-pressure regulator is installed in the
which comes in contact with the liquid may be
take-off line or lines to reduce pressure in these
frozen. If this happens, as a first aid measure, thaw
lines to the required pressure. These regulators are
the affected part immediately by applying cold
vented to the outside of the building, not under the
water or cold pads. Then treat exactly as a burn and
pilot as with natural gas. (See figure 2-3.) Furnaces
get medical assistance.
are equipped with 100-percent-cut-off valves. That
(3) Avoid leaks. LPG will ignite only when it
is, all gas, including pilot gas, is cut off if the pilot
vaporizes and mixes with sufficient air to form a
is extinguished. Furnaces with two or more pilots
combustible mixture. Vapor leaks permit such
have a separate pilotstat for each pilot, all wired in
mixtures to form. A leak will burn close to or at a
series. Each of the small solenoid valves installed in
distance from the opening, depending on the gas
the pilot line is wired in parallel with the usual main
pressure and the size of the opening.
burner electric solenoid valve. If any pilot should
(4) Comply with rules and regulations govern-
go out, its pilotstat breaks the circuit and shuts off
ing transportation, storage, and dispensing of LPG.
the gas supply for all main burners and pilots.
2-5
TM 5-642
2-6
TM 5-642