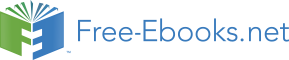

95.2
95.4
95.1
150
200
95,4
96,2
95,8
132
175
95.4
95.6
95.4
185
250
95,8
96,2
95,8
160
215
95.6
95.8
95.6
200
270
95,8
96,2
95,8
200
270
95.8
96.0
95.8
260
350
95.8
96.0
95.8
260
350
95,8
96,2
95,8
300
400
95.8
96.0
95.8
300
400
95,8
96,2
95,8
335
450
95.8
96.0
95.8
335
450
95,8
96,2
95,8
375
500
95.8
96.0
95.8
375
500
95,8
96,2
95,8
Table 7. Premium Efficiency IE3 50Hz
Table 8. Premium Efficiency IE3 60Hz
(NEMA Premium)
Annex 3. CEI efficiencies
Annex 4: Acronyms
•
ASD Adjustable speed drives
•
ACEEE American Council for and Energy Efficient Economy
•
CEE Consortium for Energy Efficiency
•
DOE Department of Energy
•
EISA Energy Independence & Security Act
•
EPAct Energy Policy act
•
EU European Union
•
GHG Greenhouse gas emissions
•
IPCC International Panel on climate change
•
OEM Original equipment manufacturer
•
MG 1 Motor Generator
•
MEPS Minimum energy performance standard MEPS
•
MDM Motor Decisions Matter (MDM
•
NEMA National Electrical Manufacturers Association
Premium Efficiency Motors
23
11. References
Aoulkadi, M., Binder, A.: “Evaluation of different measurement methods to determine stray
load losses in induction machines,”. IEEE Trans. On Industrial Electronics, vol. 2
No 1, 2008
Benhaddadi M., Olivier G.: (2010a) “La promotion de l’économie d’énergie électrique passe
par son juste prix,”. 79e Congrès de l’AFAS, Montréal, Canada, 2010
Benhaddadi M., Olivier G., and Yelle J.: (2010b) “Premium efficiency motors effectiveness,”.
IEEE International symposium on power electronics, electrical drives, automation
and motion SPEEDAM 2010, Pisa, Italy, 2010
Benhaddadi M., Olivier G., Labrosse D., Tétrault P.: (2009a) “Premium efficiency motors and
energy saving potential,”. IEEE International electric machines and drives
conference, IEEE_IEMDC, Miami, USA, 2009
Benhaddadi M., Olivier G.: (2009b) “L’économie d’énergie : une affaire de législation,”.
Communication présentée au 78e Congrès de l’ACFAS, Ottawa, Canada, 2009
Benhaddadi M., Olivier G.: (2008a) “Barriers and incentive policies to high-efficiency motors
and drives market penetration,”. IEEE International symposium on power
electronics, electrical drives, automation and motion SPEEDAM 2008, Ischia, Italy,
Benhaddadi M., Olivier G.: (2008b) “Le génie électrique à la rescousse des économies
d’énergie dans l’industrie,”. Communication présentée au 76e Congrès de l’ACFAS,
Québec, Canada, 2008
Benhaddadi M., Olivier G.: (2008c) “Dilemmes énergétiques,”. Presses de l’Université du
Québec, Québec, 2008, 216p.
Benhaddadi, M., Olivier G.: (2007) “Energy savings by means of generalization adjustable
speed drive Utilization,”. IEEE Canadian Conference on Electrical and Computer
Engineering, Vancouver, 2007.
Benhaddadi M., Olivier G.: (2004) “Including Kyoto in electrical engineering curriculum,”.
IEEE Canadian Conference on Electrical and Computer Engineering, Niagara Falls,
2004
Boglietti, A. Cavagnino, A. Lazzari, M. Pastorelli, , M.: (2004) “International standards for
the induction motor efficiency evaluation: a critical analysis o A. f the stray-load
loss determination,”. IEEE Trans. On Industry Appl., vol.40, No 5, 2004
Bonnett, A.H., Yung, C.: (2008) “Increased efficiency versus increased reliability: A
comparison of pre-EPAct, EPAct, and premium-efficiency motors,”. IEEE Industry
application Magazine, vol.2, 2008
BP (2010) British Petroleum statistical review of world energy (2010), June 2010
CEE (2007) Energy-efficiency incentive programs: Premium-efficiency motors and
adjustable speed drives in the US and Canada, (2007) prepared by consortium for
energy efficiency, may 2007, www.cee.org
DOE (2010) Energy Information Administration, Official energy statistics from the US
government,
DOE/EIA http://www.eia.doe.gov
Elmeida, A.I. Ferreira, F.FJ. Busch, J.F. Angers P. (2002) “Comparative analysis of IEEE-112 B
and IEC 34-2 efficiency testing standards using stray load losses in low-voltage
three phase cage induction motors,” IEEE Industry applications, March-April 2002,
pp. 608-614
Energy Policy Act EPACT and motor testing understanding, IEEE-112 Method B,
24
Electric Machines and Drives
Evans, B.D., Crissman, J., Gobert, G.: (2008) “Test results for energy savings,”. IEEE Industry
application Magazine, vol.2, 2008
Finlay, W.R. Veerkamp B., Gehring D., and Hanna: P. (2009)“Improving motor efficiency
levels globally,”. IEEE Industry application Magazine, vol.15, 2009
IEA (2010) International Energy Agency, OECD/IEA http://oecd.org./
IEA (2009) The experience with energy efficiency policies and programs in IEA countries:
learning from the critics, (2009) International energy agency information paper,
august 2009
IPCC (2007) Contribution of working group I to the fourth assessment report of the
intergovernmental panel on climate change, summary for policymakers,
http://www.ipcc.ch
Nagorny, A., Wallace, A., Von Jouanne, A.: “Stray load loss efficiency connections,”. IEEE
Industry application Magazine, vol.10, issue 3, may-june 2004
NRC (2004) Energy-efficient motor systems assessment guide, Canadian industry program
for energy conservation (2004), CIPEC, Natural Resources Canada, 2004
Parasiliti, F., Villani, M., Paris, C., Walti, O. Songini, G. Novello, A. Rossi T.: (2004) “Three-
phase induction motor efficiency improvements with die-cast cooper rotor cage
and premium steel,”. IEEE International symposium on power electronics,
electrical drives, automation and motion SPPEDAM 2004, Capri, Italy, 2004
RNC (2004) Ressources Naturelles Canada: (2004) “Guide d’évaluation du rendement des
systèmes moteurs éconergétiques,” RNC, 2004
Renier, B. Hameyer, K., Belmans, R.: (1999) “Comparison standards for determining
efficiency of three phase induction motors,”. IEEE Trans. On Energy Conversion,
vol.14, No 3, 1999
Rooks, J.A., Wallace: (2004) “Energy efficiency of VSDs,” IEEE Industry applications
Magazine, vol.10, issue 3, 2004
UE (2003) Commission Européenne, Direction générale énergie et transport: (2003) “Motor
challenge programme,”. UE, Bruxelles, 2003
2
Electric Motor Performance Improvement Using
Auxiliary Windings and Capacitance Injection
Nicolae D.V
Tshwane University of Technology
South Africa
1. Introduction
Generally, some electric machines such as induction machines and synchronous reluctance
motors require reactive power for operation. While the reactive power required by a
synchronous machine can be taken from the power source or supplied by the machine itself
by adjustment of the field current, the power factor of an induction machine is always
lagging and set by external quantities (i.e., the load and terminal voltage). Poor power
factor adversely affects the distribution system and a cost penalty is frequently levied for
excessive VAr consumption.
Power factor is typically improved by installation of capacitor banks parallel to the motor. If
the capacitor bank is fixed (i.e. that it can compensate power factor only for a fixed load),
when the load is variable, then the compensation is lost. Some authors (El-Sharkawi et al,
1984, Fuchs and Hanna, 2002) introduced the capacitors using thyristor/triac controllers; by
adjusting the firing angle, the capacitance introduced in parallel with the motor becomes
variable and thus compensating the power factor for any load. Other works (Suciu et al,
2000.) consider the induction motor as an RL load and power factor is improved by inserting
a variable capacitor (through a bridge converter) which is adjusted for unity according with
the load. For the above methods, the capacitive injection is directly into the supply. Another
method conceived for slip ring induction motor was to inject capacitive reactive power
direct into the rotor circuit (Reinert and Parsley, 1995; Suciu, et al. 2002).
The injection of reactive power can be done through auxiliary windings magnetically
coupled with the main windings (E. Muljadi et al. 1989; Tamrakan and Malik, 1999;
Medarametla et al. 1992; Umans, and H. L. Hess, 1983; Jimoh and Nicolae, 2006, 2007). This
compensating method has also been applied with good results not only for induction
motors but also for a synchronous reluctance motor (Ogunjuyigbe et al. 2010).
2. Method description
2.1 Physical solution
The method described in this chapter makes use of two three-phase stator windings. One
set, the main winding (star or delta), is connected directly to the source. The other set of
windings - auxiliary, is only magnetically coupled to the main winding. All windings have
the same shape and pitch, but may have different turn numbers and wire sizes; usually
smaller in order to be accommodated in the slots together with the stator. The windings are
26
Electric Machines and Drives
arranged in slots such that there is no phase shift between the two windings. Figure 1 shows
a possible arrangement of the windings for a four pole induction machine.
+A
-C
+A
-C
+A
-C
+X
-Z
+X
-B
-Z
+X
+B
-Z
-Y
-B
+Y
-Y
+B
-B
+Y
-Y
+B
+C
+Z
+Y
-A
+C
-X
+Z
-A
+C
-X
+Z
-A
-X
-X
-A
+Z
-X
+C
-A
+Z
-X
+C
-A
+Z
+Y
+C
+B
-Y
+Y
-B
-Y
+Y
+B
-Y
-Z
-B
+B
+X
-Z
+X
-B
+X
-Z
-C
+A
-C
+A
+A
-C
Fig. 1. High Power factor induction machines-windings arrangement
2.2 Auxiliary windings connections
As mention above, the main winding can have delta or star connection. Figure 2 shows the
main winding connected in star and the auxiliary windings connected in generic (a), star (b)
and delta (c) to the capacitor bank via a static switch.
Figure 3 shows a simpler way to inject capacitive reactive power. In this method, the
auxiliary windings are in “single –phase connection” with the apparent advantage of using
only one capacitor and static switch.
2.3 Variable Capacitors
In order to achieve a compensation for various loading of the machine, the compensating
capacitor should be able to be varied. This capability is obtained through connecting a fixed
capacitor via a static switch. The static switch can be achieved using thyristors or IGBTs in
bidirectional configuration.
Electric Motor Performance Improvement Using Auxiliary Windings and Capacitance Injection
27
V
Ia
a
*
*
Vx
I
V
b
b
*
●
Rotor
*
Vy
V
Ic
c
*
*
Vz
Static Switch
C
(a)
● Va
●Vb
●Vc
●
●
●
Va
Cz
Cx
●
Vx
Vz
●
●
●
●
● V
●
x
● Vy
●V
●
z
Vc
Vb
Vy
●
●
Cx
Cy
Cz
●
C
y
(b) (c)
Fig. 2. Auxiliary windings: a) generic connection; b) star connection; c) delta connection
Ia
Va
Vx
Ib
Vb
●
Rotor
Vy
Ic
Vc
Vz
Va
Iax
Static Switch
C
Fig. 3. Auxiliary windings: “single –phase connection”
28
Electric Machines and Drives
2.3.1 Thyristor-based variable capacitor
Figure 4 shows the use of thyristor to accomplish a variable capacitor. The inductor Lr is
introduced to reduce – limit the surge current; it is relatively small and does not affect the
overall capacitive behaviour.
Th2
C
L
Th
r
1
Fig. 4. Variable capacitor using bidirectional thyristor
The equivalent capacitance depends on the delay angle. Due to the phase angle control, the
device introduces harmonic currents.
2.3.2 IGBT-based variable capacitor
The above drawback can be address using IGBTs in bidirectional configuration (Figure 5)
and a switching frequency higher then operational frequency (50 Hz).
Fig. 5. IGBT in bidirectional topology
Figure 6 shows a configuration to achieve a variable capacitor using two bidirectional static
switches. The main capacitor C1 is introduced in the auxiliary winding circuit, via a
bidirectional switch Sw1, for a period of time depending on the duty cycle (δ) of the
switching frequency; in this time the bidirectional switch Sw2 is OFF. When Sw1 is OFF, the
capacitor is discharged. The reactor Lr limits the capacitive surge current without affecting
the capacitive behaviour.
●
Ix
Sw1
Lr
●
Vx
C
Sw
2
C1
2
●
●
Fig. 6. Variable capacitor using two IGBTs in bidirectional topology
Electric Motor Performance Improvement Using Auxiliary Windings and Capacitance Injection
29
The capacitor C2, much smaller than C1 is connected to mitigate the voltage spikes during
switching off the main capacitor. Thus, the equivalent capacitor can be written as:
C =δ×C +C (1)
eq
1
2
2.3.3 Variable capacitor H-topology
Figure 7 shows a single-phase H topology to achieve a variable capacitor. This
configuration using H-bridge bidirectional topology obtains a higher equivalent capacitance
for the same fixed one as reference. In this configuration, the reactor Lr has the same
purpose of limiting the surge capacitive current, while C2 also of small value mitigates the
voltage spikes. The equivalent capacitance could be express as:
C
1
C =C +
(2)
eq
2
(2δ )2
-1
It can be notice that the equivalent capacitance could increase significant when the duty
cycle approaches 50 %. In practice, the switches are not ideal and there is no “infinite
increase” of the equivalent capacitance.
Vx
Ix
●
●
C2
●
Sw1
Sw2
Lr
●
●
C1
Sw3
Sw4
●
Fig. 7. Variable capacitor using H-bridge bidirectional topology
Ix
Iy
C
Iz
Fig. 8. Variable capacitor using three-phase H-bridge topology
30
Electric Machines and Drives
Another solution to achieve a variable capacitance, or rather to generate a capacitive current
was proposed using a three-phase H topology as PWM inverter (E. Muljadi, et al 1989;
Tamrakan and Malik, 1999) as presented in Figure 8. The converter injects capacitive
reactive power into auxiliary windings and thus improving the power factor of the motor.
3. Mathematical model
The machine is treated as having two three-phase windings and the voltages equations
system can be written as:
d
[V ]=[R ][I ]+
[λ ] (3)
abcs
1
abc
abc
dt
d
0=[R ][I ]+
[λ ]+Vc (2)
2
xyz
xyz
xyz
dt
d
0=[R ][I
]+
[λ
] (5)
r
abcr
abcr
dt
where
T
V =⎡⎣V V V ⎤
abc
a
b
c ⎦ (6)
T
I
= I
⎡⎣
I
I ⎤
λ =⎡⎣λ λ
λ ⎤
abcs
a
b
c ⎦ ;
T
abc
a
b
c ⎦ (7)
⎡r
0 0 ⎤
⎡r 0 0 ⎤
a
x
⎢
⎥
[R ]= ⎢ 0 r
0 ⎥ [R ]=⎢0 r 0
(8)
1
⎢
b
⎥
2
y
⎥
⎢ 0 0 r ⎥
⎣
⎢
⎥
c ⎦
⎣ 0 0 rz ⎦
Note that indices “1” refer to the main winding and “2” to the auxiliary winding.
⎡λ ⎤ ⎡ L
L
L
⎤ ⎡
⎤
abc
abcsxyz
abcsr
I
abcs
abcs
⎢
⎥ ⎢
⎥ ⎢
⎥
⎢ λ ⎥=⎢L
L
L
⎥ ⎢I
(9)
xyz
xyzabcs
xyz
xyzabcr
xyz ⎥
⎢