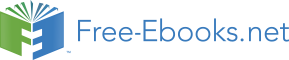

Hearing Protection
1. The company supplies hearing protection for all employees. Ear muffs and plugs can be obtained from your supervisor.
2. If you are working in an area where you feel the noise level is bothering you, use hearing protection. The noise level changes in the shop depending on the job, protect your self by using hearing protection.
3. Any person operating a hand grinder or large impact tools must use hearing protection. Cotton does not serve as an adequate hearing protection. Be sure to get the proper fit on the earplugs.
4. Alert your co-workers in your area if you are going to be generating a noise level above the normal workplace level so they can also be prepared to use hearing protection.
Eye Protection
1. Safety glasses with side shields are required by every employee, customer or visitor entering any area that exposes the eye to hazards from flying particles.
2. A face shield and safety glasses with side shields must be used when doing grinding of any type or when using wire wheel buffers.
3. Face shields and goggles should be cleaned after use.
4. Damaged face shield and goggles will be removed from services and replaced by a good set immediately.
5. A welding helmet with tinted face shield and safety glasses with side shields must be worn when welding to protect eyes from light, sparks and radiation.
Lifting
1. Always check the weight of the load before you attempt to lift. If the load seems too heavy, get help. DO NOT LIFT ANYTHING YOU FEEL IS TOO HEAVY.
2. Position yourself as close to the load as possible. The further you hold the load from body, the heavier it will be on your spine.
3. Assume a wide base of support, with legs shoulder width apart and one foot slightly ahead of the other. A wide base of support will ensure a better balance and keep your knees from getting in the way.
4. Keep the normal curves in your spine. Keep your head up!
5. Keep your stomach muscles firm. This will prevent you from overarching your back while lifting.
6. Use smooth, controlled movements, do not twist, move feet first. Rapid or jerking motions can place increase demands on your back.
Head Protection
1. Head protection shall be worn in areas where applicable.
2. Head bands of hard hats shall fit snugly, and shall be adjustable.
3. There shall be sufficient clearance between the shell of the hard hat and the suspension.
4. The hard hat shell shall be kept clean and shall be inspected for any defects such as cracks, dents or worn spots.
5. Hard hats shall not be left sitting in direct sunlight or in extreme heat areas as damage may occur to the shell.
6. Hard hats shall not be altered in anyway.
7. Hard hat suspension systems shall be maintained and replaced as needed.
Hand Protection
1. Hand protection shall be worn where applicable.
2. Hand protection shall fit well enough to allow proper dexterity for the job being performed.
3. Hand protection shall be kept clean and free from chemicals or oils.
4. Hand protection that has been contaminated by chemicals, oils or greases should be either decontaminated or disposed of.
5. Hand protection shall be kept free from damage or tears.
6. Hand protection shall be worn when handling materials that maybe abrasive, or may have burrs.
7. When handling extremely coarse or abrasive materials special precautions shall be taken to use proper gloves for job being performed.
Foot Protection
1. Foot protection shall be worn where applicable.
2. Foot protection shall be determined by the type of job being performed as to type of foot wear required such as: safety shoes or boots or foot guards.
3. Safety foot wear shall be kept clean and inspected regularly for any defects such as: torn, loose soles or cracked or torn toe protection.
4. Safety shoes or boots shall fit so that the equipment does not cause unusual tiring or irritation.
OUTSOURCING
Outsourcing can not be overruled in today’s context. The capacities of the mines are increasing day by day with rapid technological advancement. Some works/ services are outsourced due to the following:
Shortage of required equipments.
Shortage of Manpower.
Cost effectiveness.
Safety is the major concern in outsourced works/ services due to the following:
Big Contractors sub-let parts of their Job to petty Contractors not having adequate capacity or concern for safety.
The employees of contractor are purely temporary or migratory in nature. The workers are not well conversant with mining activities or laws.
On most cases the workers are not at all trained for the Job.
The workers are having more risk taking attitude as earnings directly connected with output.
The contractors consider safety as a cost component only, ignoring the cost of lives or living conditions.
These issues need special attention at the initial stages so that it does not affect the objective of the mining industry.
Indian mining is gradually shifting from the existing prescriptive legislation to a goal setting legislation meant for self regulation by
implementing Safe Operating Procedure as recommended in 10th National Safety conference.
Sample Safe operating Procedure (SOP) on
Outsourcing
1.0 The Principal Employer
The Principal employer should depute a representative who will determine whether or not the contractor is complying with the contractual obligations.
Employer shall ensure that contractor provide the machinery, operator and other staff with written safe work/ operating procedures for the work to be carried out, stating clearly the risk involved and how it is to be managed.
The employer shall circulate relevant portions of statute applicable to contractors including abstract of mines Act-1952 to all the contractors.
The employer shall circulate sample ‘Safe Operating procedure’
for different equipment, works and services, so that the contractor is able to prepare and implement the SOP.
The employer is required to approve the SOP prepared by the contractor after necessary modification if required, depending on the type of equipment, work and service.
In case non adherence to safety/ health requirements by contractor /his workmen to issue spot safety violation memo and recommend for penal action as per agreement with the contractor.
2.0 The Contractor
The contractor should ensure to appoint a responsible person before commencement of work with regard to any Contract.
The authorized person who has signed the Contract shall only appoint this representative.
Such authorised person should be available on the site for all purposes and to supervise, take ownership and be responsible for all work carried out on premises / workplace by the concerned contractor's employees.
Ensure that all the personnel going to work on the site of the Company to carry out the works defined in the Contract, are VT
Trained.
Provide all the relevant personal protection equipments to all the personnel of the contractor at their own cost.
No personnel of the contractor should enter the site and/ or carry out the work without wearing the personal protection equipments.
Prepare written Safe Operating Procedure (SOP) for the work to be carried out, including an assessment of risk, wherever possible and safe methods to deal with it/them and get it approved from the principal employer.
Ensure that all work is carried out in accordance with the Statute and SOP and for the purpose he may deploy adequate qualified and competent personnel for the purpose of carrying out the job in a safe manner.
Ensure that all sub-contractors hired by him comply with the same requirement as the contractor himself and shall be liable for ensuring compliance of all safety laws by the sub or sub-sub contractors.
All persons deployed by the contractor for working in a mine must undergo vocational training, initial medical examination, PME.
All employees should be issued identity cards stating the name of the contractor and the work and its validity period, indicating status of VT & IME.
Every person deployed by the contractor in a mine must wear safety gadgets to be provided by the contractor.
The contractor shall submit to DGMS returns indicating - Name of his firm, Registration number, Name and address of person heading the firm, Nature of work, type of deployment of work persons, Number of work persons deployed, how many work persons hold VT Certificate, how many work persons undergone IME and type of medical coverage given to the work persons.
The return shall be submitted quarterly (by 10th of April, July, October & January) for contracts of more than one year.
3.0 Contractor Employee
An employee must follow Regulation- 38 of Coal Mines Regulation (CMR) 1957.
An employee must, while at work, take reasonable care for the health and safety of people who are at the employee’s place of work and who may be affected by the employee’s act or omissions at work.
All assaults shall be reported immediately to the company responsible person. People in the assault could be suspended form premises.
It is a sample Safe Operating Procedure (SOP) and to be modified as per specific requirement.
OB IN THE DUMP/ YARD/ STOCKPILEAS
1-
All overburdens removed by shovel-dumper combination shall be dumped only in the specified dump yards maintained for the purpose and in a stable condition.
2-
No operator shall dump any overburden materials in the coal dump yard or on the haulroad or at any other place.
3-
The speed of dumper while going to dump yard form haulroad should not exceed 15 kms/hour. Also dumper operator should blow hom. Same procedure should be adopted while coming back from dump yard to haulroad.
4-
On entering a dump yard the dumper operator should take due care in positioning of dumper’s near wheels.
5-
In dump yard as far as possible lighting towards of adjustable height should be installed to avoid any chances of dumping made near/ directly beneath an electric over had line/lighting tower.
6-
At the edge of dump yard safety berm shall be provided , Height & width of berm should not be less than one metre.
7-
Dumper’s dumping over the berm shall back up squarely to the berm . After positioning the vehicle for dumping, the dumper operator shall release the hoist with the vehicle in stationary position. Hoist must be completely lowered after dumping operation has been completed.
8-
The reversing speed of dumper for dumping shall not exceed 10 Km/hour.
9-
The dumpers shall be filled, with operative AVAs.
10-
Dumpers operating between sunset & sunrise shall be fitted with rear flood light of sufficient illumination capacity provide & clear vision for a distance not less then 10 meters.
11-
Shift Overman / mining sirdar / Foreman shall inspect the dump yard at least twice i.e. at the beginning of the shift and at the end of the shift apart from emergency inspection of the dump yard after rains etc. Inspection by other officials: will be as under-Asstt. Manager / safety Officer - Thrice a week atleast Shift Manager / - At least once during shift Manager - At least once a week 12-Water spraying or other arrangement for dust suppression shall be done in a dump yard.
13-
Dump yard shall be maintained as level as possible. Gradient at entry to the main dump yard shall not exceed 1 in 20.
14-
Adequate drainage shall be provided.
15-
Non operational areas or unstable surfaces or edges shall be adequately fenced.
16-
If at any time the operator considers the operation unsafe this shall be immediately reported to Manager / Incharge of Excavation / Foreman / overman
/ Mining Sirdar .
IMPLEMENTATION ;
17-
The copy of the code shall be given to such dumper dozer operator and to the concerned supervisory shift/ officers.
18-
Employees / operators / supervisors at stockpiles / dumps shall immediately report unsafe condition at the stockpiles / dumps and of mobile
equipments to the mine managers / Incharge of excavation Foreman / overman /
Mining Sirdar.
Machinery
Do not operate any machinery without complete and clear instructions from your supervisor. It is his/her responsibility to make certain that each employee knows and understands the proper operation of the machine as well as any potential hazards involved. If you have any questions or doubts what-so-ever about the hazards or operation of any machine, do not run it before your supervisor has answered your questions. Since machine-related accidents are usually very serious, any written rules or supervisor’s directions which are not explicitly followed will result in strong disciplinary actions.
1. The motor safety switch must be OFF before you work on a machine. The safety switch should be locked and tagged off, if the machine should not be started. This is the only way to prevent an accident if someone should accidentally brush or press against the starting button or lever.
2. No machine should be oiled, cleaned or adjusted while it is in operation unless specific provisions have been made for this purpose.
3. Safety devices should not be by-passed, blocked or tied down.
4. The safety interlock should never be used as a starting device.
5. Guards are placed at all hazardous points on the machine. They must be in place when the machinery is in operation. When this is not the case, a supervisor signed Danger Tag with printed operating instructions must be posted on the unguarded area and on the safety switch. The department head and safety officer must be duly informed.
6. If, of necessity, a guard must be removed and the machine power operated, keep a safe distance. Never attempt a repair or adjustment in an area that cannot be reached safely.
7. Don’t make any alterations on your own. Tell your supervisor if you feel a guard needs changing.
8. You may make only those operating adjustments stated in the machine operation instructions. You must shutoff the safety switch and lockout the MCC if you are going into an unguarded area.
9. When you leave your machine, shut OFF the safety switch. No machine should be left running unattended unless specifically designed for that purpose. If the machine should not be operated, be sure to tag and lock the safety switch OFF.
10. Wait for the machine to stop! Do not try to slow down or brake a moving machine by hand or with a makeshift device. If there is a problem, notify your supervisor. He/she will inform the proper authorities.
11. Before clearing a jam be sure to turn the safety switch OFF unless there are other written procedures from the Safety Department.
12. Make sure everyone is clear of the machine before you start it.
13. Adjusting tools or keys should not be left in places where they can fall, slide or be thrown into the machine when it is started.
14. Only use those machines and equipment for which you have been trained and authorized.
15. Do not wear jewelry, gloves, neckties, long sleeves or loose clothing around machines. Hair should not be loose or straggly. Revolving shafts can catch onto these. Extreme caution is always necessary around running machinery.
16. Machines should always be clean and free of rags, tools or other devices. The floor around the machine must be clean and dry to avoid stumbling, slipping or bumping.
17. Use the proper brush, hook or tool to remove residue such as chips or shavings. Never use your hands or an air hose.
18. Transparent guards must be clean at all times.
19. Do not use pins, projecting set screws, etc. on rotating parts unless properly guarded.
20. Use special tools such as pliers, push sticks, hooks, etc. Keep fingers and hands clear of operating surfaces.
21. Report all hazards to your supervisor.
Machine Guarding
1. Regulations clearly state points of operation and power transmission shall be guarded.
2. Guards shall be affixed to the machine where possible and secured elsewhere if for any reason attachment to the machine is not possible.
3. Guards shall be so designed that they do not create an accident hazard in themselves.
4. Guards shall be so designed and securely mounted to provide adequate protection.
5. All belts, pulleys, gears and chains shall be properly guarded.
6. Fans and fly wheels within seven feet of the floor or ground level shall be guarded. All fan guards shall have openings no larger than ½ inch.
7. Shafts and shaft ends shall be guarded.
8. Guards on grinders shall cover the spindle end, nut and flange projections.
Bench grinders shall have properly installed work rests.
9. Machinery and power tool guards will be inspected regularly to be sure that they are securely in place and properly aligned.
10. Moveable guards will be inspected and maintained periodically to be sure that they are in good operating condition.
11. Guards removed for repairs or maintenance shall be remounted before the machine or power tool is put back into operation.
12. Machines designed for fixed location shall be securely anchored to prevent walking or moving.