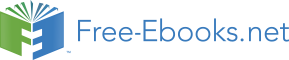

PLEXFORM
PACKAGING
SERVICES INC.
5 Amazing Design Solutions To Optimize
Logistics, No Matter The Volume Size!
Plexform Packaging Services Inc.
1
5 Amazing Design Solutions To Optimize Logistics, No Matter The Volume Size!
Copyright @2020 by Plexform Packaging Services Inc.
All rights reserved. No part of this publication may be reproduced, distributed, or transmitted in any form or by any means, including photocopying, recording, or any other electronic or mechanical methods, without the prior written permission of the publisher, except in the case of brief quotations embodied in critical reviews and certain other non- commercial uses permitted by copyright law.
2
INTRODUCTION ...................................................................................... 4
CHAPTER 1: DETERMINING THE BEST CONTAINER OPTION .................. 5
CHAPTER 2: COMMON MATERIALS UTILIZED ........................................ 9
CHAPTER 3: BEST METHODS TO LAUNCH A DESIGN ............................ 13
CHAPTER 4: GENERATING CONCEPT MECHANICAL PRINTS ................. 18
CHAPTER 5: FIVE AMAZING SOLUTIONS TO OPTIMIZE LOGISTICS ...... 22
CHAPTER 6: REVIEW AND SUMMARY .................................................. 29
3
When it comes to logistics in regards to shipping manufactured component parts, it’s essential that a custom packaging design is produced specifically tailored to each unique part. The holding mechanisms used in all designs shall hold the part firm while in transit thus allowing the product to arrive safely to its destination.
The quantity of manufactured component parts (known as density) each package shall occupy is totally depended on the size, shape, texture, and weight of the part. In some cases, the customer will issue a target density to acquire, therefore, limiting the amount the package will hold to a specific quantity (even if you can achieve a higher quantity).
Every component is treated different when it comes to packaging. Some parts require additional protection due to the part being extremely delicate, while other parts require little to none. Weak points on a component are also taken with vigilant measures, as these areas are to be avoided when designing and building the holding mechanism in the package.
In this report, we will illustrate 5 amazing various methods to optimize logistics.
Efficiently shipping a bulk quantity of manufactured component parts safely from point A to point B can save any company a large sum of money, either from avoiding expensive product damage or successfully delivering an above expectations quantity amount.
4
CHAPTER 1: DETERMINING THE
BEST CONTAINER OPTION
5
The overall size of the package will be determined by the size of the part and the target density (the larger the part with a higher target goal consequently means the larger the package will be).
There are many different material handling container options to choose from when you need to accommodate for the part size:
1. Hand held plastic tote container
Small parts are recommended to be assembled and packaged in hand held tote containers.
Typically there will be Interior dunnage designed and manufactured and fastened inside the container to secure the component in transit.
Plastic corrugated dividers are the common choice to separate parts in the container during the loading process. Other options like fabric inserts can also be utilized to create pockets for each part (known as cells).
Container sizes vary but the most common size utilized is the 24” (Length) X
22” (Width) due to its efficient storage capacity when loaded on pallets.
These containers are stacked high to achieve a greater volume.
6
2. Custom size tote container
In addition to the various standard size tote containers, a custom size tote can be assembled to accommodate non-standard size containers.
Stacking corners are incorporated in all custom built containers to enable the stacking function for optimal storage results.
3. Bulk bin plastic container
Large parts are recommended to be assembled and packaged in bulk containers.
The bulk containers have a wide variety of selection when it comes to overall sizes but the most common size utilized is the 48” (Length) X 45”
(Width) X 50” (Height) due to its efficient storage capacity when fully loaded in a truck. These containers are stacked high to achieve a greater volume.
There is a top load and side load options with the top load being the more cost effective solution.
The bottom of these bins contain pockets for the forklift forks to enable easy movement and stacking of these containers.
Interior dunnage such as crosslink foams, plastic corrugated sheets and fabric inserts are the best choice for the bulk bins when producing the holding mechanism.
7
4. Custom steel fabricated racks
Small and large parts can both be a great fit in a uniquely designed and fabricated custom rack.
Any size can be manufactured to assure the best fit possible.
However, a common width dimension is 48” to effectively place these racks side to side in the freight trailer.
The stacking caps on top of the corner posts enable these racks to stack high to achieve a greater volume and optimize storage space in all facilities.
Fabric bags, vacuum formed trays, HDPE/UHMW plastics, and formed channels with XLPE foams can be used to create the holding mechanism for various component parts.
The bottom of these racks typically contain pockets for the forklift forks to enable easy movement.
8
CHAPTER 2: COMMON
MATERIALS UTILIZED
9
The materials utilized in all designs are essential to achieve a reliable and robust package. High quality materials along with substantial fabrication and assembly provides durable and long lasting packaging for the future years to come.
There are a variety of selections implemented to build any material handling product, see below for all examples:
Steel (hot rolled steel, hollow structural sections, round bars, etc.): UHMW (ultra-high molecular weight polyethylene plastic): 10
HDPE (high-density polyethylene plastic):
Vacuum formed trays:
11
XLPE (cross-linked polyethylene foam):
Corrugated plastic sheets (directional corrugated sheets): Conpearl (non-directional polypropylene sheets): 12
CHAPTER 3: THE BEST METHODS
TO LAUNCH A DESIGN
13
The preferred design software utilized for producing these amazing solutions is Solidworks. This software enables all users to accurately optimize the density for each package, no matter the shape or size. There are a few ways to initiate the design phase when acquiring data from the customer: 1. Obtain customer cad data (preferred method)
When the customer successfully supplies the cad data (a 3d model for the manufactured component part) they want packaged, the design engineering team will then commence to load that part in the software (Solidworks).
The package design will be built around the contour of the supplied part and with accordance to the requirements specified by the customer.
2. Receive dimensions of the manufactured component part
Obtaining dimensions can also be an effective method to achieve an optimal package.
The customer part can be designed with the dimensions provided and plugged into the overall assembly design to determine accurate results.
3. Collect an existing physical part for reverse engineering.
If a physical part can be provided by the customer, then the supplier can measure the part and gather all the dimensions.
Once all the dimensions are collected, the design can be built around the shape and size of the part to once again achieve accurate results.
The bonus advantage to this method is that the part fit can be tested immediately by the supplier once the prototype of the package is manufactured to assure proper part fit.
14
Here’s an example of the step one preferred method (design from obtaining customer cad data):
Receive CAD Data and requirements:
Produce a concept design to maximize density (in this case the part is orientated vertically along 2 rows resulting in the best and efficient overall quantity): 15
Input cad data into the rack design to determine the density and part fit: For this particular case, part contact is insignificant which results in close contact loading to maximize density. If the part contact was impermissible, then there would need to be a barrier between parts to separate them in the loading and unloading process, thus achieving less density.
As previously mentioned, the pockets in the base enable easy movement when the forklift forks enter the pockets and lifts this rack to transport wherever permissible.
16
The “stacking caps” welded on top of each corner permits the ability to successfully stack one rack on top of another. This critical feature optimizes the storage capabilities and since this particular rack is 50” tall, it allows for 2 racks to be stacked vertically and loaded simultaneously in a standard 53’ freight trailer (the inside height dimension of the freight trailer is typically around 102”).
Stacking vertically also optimizes warehouse storage, consequently allowing companies extra floor space for other commodities.
The “part retention caps” located in front of the cantilever steel structures provide a holding mechanism for these specific parts once loaded, thus preventing the parts from falling out during transit.
17
CHAPTER 4: GENERATING
CONCEPT MECHANICAL PRINTS
18
Once a design is created and approved by the customer after following all requirements and having provided innovative solutions, a completion for a mechanical print is commenced as a concept drawing is essential for the manufacturing process.
Basically all designs require mechanical prints to help aid the manufacturing building process. It’s nearly impossible to build any sort of appliance just by providing an image with no dimensions, no list of materials and no directions.
The design engineering team will produce a concept print fully illustrating how the package is assembled. Large assemblies will be broken down into smaller sub-assemblies to simplify the building process and all items shall be identified with a numerical sequence system.
A bill of materials list will be located in any mechanical print created because it’s essential to any successful build. It illustrates all materials utilized in the design following with all individual item dimensions, purchased items, quantities, and descriptions.
After all sheets are completed for the concept print with all required dimensions included on each sheet and approved for build, then all the necessary sheets will be printed and bundled into one comprehensive package for the manufacturing team.
On the next page there is an illustration example of a partial concept print to give you a better understand……
19
The bill of material list shows all the individual parts and sub-assemblies required for this design.
The balloons use a numerical sequence system (1, 2, 3, etc.) and they indicate where all the parts and sub-assemblies are located.
The dimensions illustrate the accurate sizes for determining full packaging optimization.
THE BASE SUB-ASSEMBLY (BALLOON #1) IS SHOWN ON THE NEXT PAGE
FOR ILLUSTRATION PURPOSES.
20
This is a sub-assembly sheet for the base sub-assembly (balloon #1).
These type of sheets are necessary to simplify the manufacturing process.
It’s a lot easier to read prints when all the dimensions and individual items are not crowded in one sheet.
The bill of materials list on this sheet is more specific than the previous sheet. It clearly states the quantity required for each item and the full item description (item names like “HRS” hot rolled steel and “HSS” hollow structural section along with all sizes).
All these items need to be ordered accordingly and processed for build. The raw materials typically don’t come to size, therefore, sizes need to be cut to length, flat sheets that require bending need to be formed, etc.
21
CHAPTER 5: FIVE AMAZING
SOLUTIONS TO OPTIMIZE LOGISTICS
22
There are a variety of innovative solutions to optimize packaging and logistics. The greater the amount of component parts transported in one fleet from one location to another can save significant costs for any company.
Designing and manufacturing interior packaging dunnage for large bulk bin containers, small hand held container totes and custom steel racks will effectively increase product safety, improve warehouse floor space and decrease logistics costs.
The fundamentals to a successful design and build consists of excellent communication between customer and supplier along with meeting all deadlines within an agreed timeframe.
When a customer sends an RFQ (request for quote) to the supplier for a certain packaging build, the supplier then sends a quote with all costs included along with a lead time (the time duration for completion). All projects are not treated equal as it can take a lot more time and effort to complete an advanced complex design as opposed to a simpler package.
Please check out the following pages as there are 5 amazing solutions to optimize logistics that are illustrated…….
23
1 . COLLAPSIBLE RACK
Collapsible racks serve the same purpose as any other standard racks, but these particular racks have the ability to fold down when the parts are unloaded.
The advantage of the folding capability is that it increases the stacking quantity amount in the freight trailer.
These are a great option when returning racks because the collapsible feature enables increased storing efficiency during transportation.
Steel collapsible racks are durable and robust and can carry a heavy load.
The overall footprint and height can be customized to fit any requirements.
The foam dunnage utilized in this example below is the holding mechanism for the component part and they’re removable, consequently allowing the folding feature to be successfully executed without interference.
24
2 . TWO SIDED BAG FRAME MOUNTED ON DOLLY
A standard bag rack typically has bag inserts that can only be loaded and unloaded from one side. The advantage for this 2 sided bag frame mounted on a dolly is the ability to load and unload on 2 sides as opposed to 1. This dramatically increases part density and optimizes logistics.
The main function that enables the 2 sided loading feature is the swivel bearing that the steel frame is mounted on. It allows the frame to rotate 360 degrees and helps the operator to load all parts on both sides (operator will need to rotate the frame 180 degrees to access the opposite side).
A locking mechanism is installed on each opposite corner to ensure the steel frame will come to a stop once rotating the frame 180 degrees.
Bag carts enable easy mobility for operators without the need of a forklift within a manufacturing plant due to the caster wheels.
The Fabric bags are typically made from 18 oz. vinyl material reinforced with webbing for extra strength, which results in a reliable and firm solution for the component part holding mechanism. They contain pockets (referred to as cells) where the component parts will rest in.
25
3 . BULK BIN INTERIOR DUNNAGE
While there are numerous combinations to building interior bulk bin container dunnage, the most common methods typically consists of utilizing plastic corrugated sheets and cross linked foams.
As shown in the top load bulk container example below, the cross linked foam rails are waterjet cut to the exact size and shape and fastened to the plastic corrugated base (known as base pads).
4 LB. cross linked foam rails is the typical choice for most projects, but 6 LB.
or 8 LB. cross linked foam rails are necessary if extra strength is required.
In this particular case, the base pads are bent to a “V” shape with a hot wire bender to allow the foam rails to be assembled on an angle to accommodate for the “wheel flare” component.
The bend in the base pads enable 3 layers of assemblies to be placed in the bin, ultimately allowing a higher density for optimal logistics results.
Bulk containers usually come in many different options and footprint sizes to accommodate all your needs.
26
4 . CANTILEVER RACK
Cantilever racks are essentially a steel frame with extended tubes in the center for the parts to rest on.
This is a cost effective solution as it requires less steel structure in comparison to other complex custom steel racks.
The component parts can be stacked together during the loading process, consequently allowing a higher density and optimizing logistics.
The stacking caps on top of each corners enable the stacking feature and the bottom fork tubes enable easy material flow movement.
27
5 . BAG RACK WITH DIFFERENT SIZE POCKETS
Bag racks can accommodate for all types of part shapes and sizes.
The advantage these style of racks have is the capability to hold multiple variant component parts with ease.
If a program requires multiple parts to be loaded and unloaded simultaneously at a work station, then this method can provide an exceptional solution.
As shown in the images below, the large cell is holding the large red component and the small cell is holding the small green component. This 2
cell method salvages the need for 2 separate packaging builds as it carries both parts, even though the shapes and sizes are noticeably different.
The customer can save time and money with avoiding multiple design and build programs with this optimal solution.
28
CHAPTER 6: REVIEW AND
SUMMARY
29
The importance of an excellent design engineering firm is critical to optimize and save capital in the transportation and logistics budget for any company.
Our design engineering team at Plexform Packaging Services Incorporated have successfully completed and managed hundreds of projects in this sector and are fully capable and confident to instantly deliver value to any small to large size company.
Facilitating the customer’s pain points and issues is our main objective.
Providing innovative solutions to all problems our customers face in regards to packaging and logistics is our most valuable asset for any small to large size company.
Optimizing logistics is our core passion here at Plexform Packaging Services Incorporated and we enjoy growing and learning with extraordinary talent spread around our industry.
Developing customer relationships is essential to our growth so we make sure that customer satisfaction is a top priority.
Our understanding of the pressures our customers face with deadlines and precise timing for project completion is why we thrive off completing and delivering projects in a timely manner.
We help our customers maintain a competitive edge by providing innovative design solutions, improving manufacturing processes and decreasing lead times.
30
The examples shown in this report are a small sample size of the various innovative solutions to many packaging program issues. To view our full design gallery please visit https://plexformps.com/product-designs.
Also, you can view our awesome 3D automated video that illustrates packaging designs at https://vimeo.com/482006414.
For a limited time only, we’re offering an introductory FREE design service for new customers (total value ranging from $1500-$3000).
For any inquires on packaging solutions or to speak with one of our staff members, please contact us at sales@plexformps.com or toll free at +1-866-501-7111.
31
Reads:
290
Pages:
54
Published:
Feb 2024
Unlock your entrepreneurial potential with 'The Part-Time Entrepreneur: The Complete Guide To Starting Your Own Side Hustle.' This comprehensive guide provide...
Formats: PDF, Epub, Kindle, TXT